この記事ではPLCソフト設計におけるルール作り・標準化について全体の流れ(構成)をルール化するメリットと具体例について解説していきます。
目次
”全体構成をルール化”とは
結論としまして、「異常・工程・出力・各種工程間ハンドシェイクなどの全体の流れの順番をルール化する」ことです。
会社で作成手順や標準化されたものがあればいいのですが、そういったものが無い所も多く存在すると思います。むしろ実際に”標準化”と銘打ってやっているところは本当に少ないと思います。
流れとして、先輩や上司から教わるやり方をそのまま引き継いで、それが会社としての暗黙の了解みたいになっているところが多いかと思います。
では本当に何もルールが無い場合は、実際に何をルール化して行けばいいのか?というところにスポットライトを当てて解説していきたいと思います。
標準化については過去に記事にさせていただきました。
-
-
【あなたの会社は?】PLCソフトのルール作り・標準化について ポイントを解説します
この記事ではPLCソフト作成のルール作り・標準化について、ポイントや具体的に何を標準化していくとよいのか?そういった疑問に答える形で解説していきます。 そもそも標準化って 早速ですが、私なりに噛み砕い ...
続きを見る
その中でラダーを作成する上でルール化する際に、大きくこの4つに分類することが出来るとお伝えしました。
①全体の流れのルール化
②アドレスのルール化
③コメントのルール化
④各工程の構造のルール化(変数化、ファンクションブロック化して運用)
今回はその中でも「①全体の流れのルール化」について具体的に解説していきます。
なぜ”全体の流れを標準化”するのか
まずラダーを書く上で、構成の順序がある程度ルール化されていないと、この先の他のルールを決める際に弊害が出てきます。その意味ではベースの部分になるので重要な部分です。
どのような弊害が出るかを挙げると
①引継ぎ時に時間を要す
②順番が定まっていないと事故が発生したりして安全性を脅かす可能性がある
③各工程の構造をルール化する時に影響が出る
「順番のルール化以前にラダーの走る順番が分かってたら、そんなの当たり前でしょ」と思う方もいらっしゃると思いますが、自分の中でルール化していない方のパターンも幾度となく見てきました。
何が言いたいかと言いますと、残念ながら基礎を押さえずに設計されている方がおられるということです。
ディスるつもりはありませんが、残念ながら毎度ここをバラバラに設計し、不具合を連発している方もいらっしゃいます。引き継ぎで手直しすることがあるのですが、不具合を深堀りすると、ここに行きつくことが多いです。
逆に言いますと、ここをきちんとルール化すれば不具合を起こすリスクの回避につながっていきます。
という事で、ルール化することにより どのようなメリットがあるのでしょうか?
①構成順が決まっていると、ラダーの書き方そのものを統一しやすい
②装置の動作品質の改善につながる
③設計時間が短縮できる
なぜこれらがメリットになるのか説明していきます。
構成順が決まっていると、ラダーの書き方そのものを統一しやすい
アドレス・コメント・各工程の構造をルール化しても、ここの基礎的な部分が出来ていないとそもそも崩壊します。
装置の分野にもよりますが、搬送機系でしたら大型化しても、ラダーの上から下へ走る順番をブロック単位で決めていけるかと思います。
私の場合、5Kステップ級の装置から200Kステップ級の装置まで、順番は異常処理から始まり~初期設定・・・と大枠では規模に関わらず統一しています。
装置の動作品質の改善につながる
例えば、流れを理解せずに工程・出力・異常処理の順序で作成してしまった場合、異常発生後に工程を止めるまで1サイクルかかったり最悪の場合は異常発生後に工程が一つ先に進む可能性があったりします。
分野にもよると思いますが、最初にこのような不具合事例をつぶしたうえで共通化できる項目を定め並べていくことで、最終的には動作品質の改善につながっていきます。
設計時間短縮につながる
ルールに当てはめて行くので、毎度イチから全部考える必要が無いので設計時間の短縮につながります。もちろん案件や分野によっては今までとイレギュラーなパターンも出てくると思います。
また、ルール化はアップデートが伴います。その手間はあるかと思いますが、品質面や安全面、時間面からもいいことづくめなのでやる価値は十分にあると考えます。
どのようにルール化していくか
まずは装置の仕様を明確にするところから始まります。
次にルール化された流れから、必要な順序をピックアップするように進めていきます。
私の場合は特に指定がなければ、ざっくりと「異常・工程歩進・計算・出力・各種工程間ハンドシェイク」の順番で組んでいます。この順序に当てはまらないものは除外。といった感じでベースから切り抜いていきます。
手法としては「1プログラムで上から順番に走らせる」、「プログラム分けして、走らせる順番を定義しておく」などやり方はありますが、私の場合プログラム分けして、走らせる順番を定義しておく」形で設計しています。
新しいパターンの装置が来たら、それに合うように実績からアップデートします。積み上げると幅は広がりますが、実績を積み上げた結果から操作していく方がリスクの軽減ができます。
もちろん異常や工程歩進の中身もルール化して進める必要がありますが、それは別の記事で詳細を説明していきたいと思います。
まとめ
今回の記事を要約するとこんな感じです。
ポイント要約
①全体構成のルール化とは異常・工程・出力・各種工程間ハンドシェイクなどの全体の流れの順番をルール化すること
①構成順が決まっていると、ラダーの書き方そのものを統一しやすい
②ルール化することで装置の動作品質の改善につながる
③設計時間が短縮でき、安全面や不具合に対するアプローチが盛り込める
④アップデートからの積み上げを惜しまずにおこなう
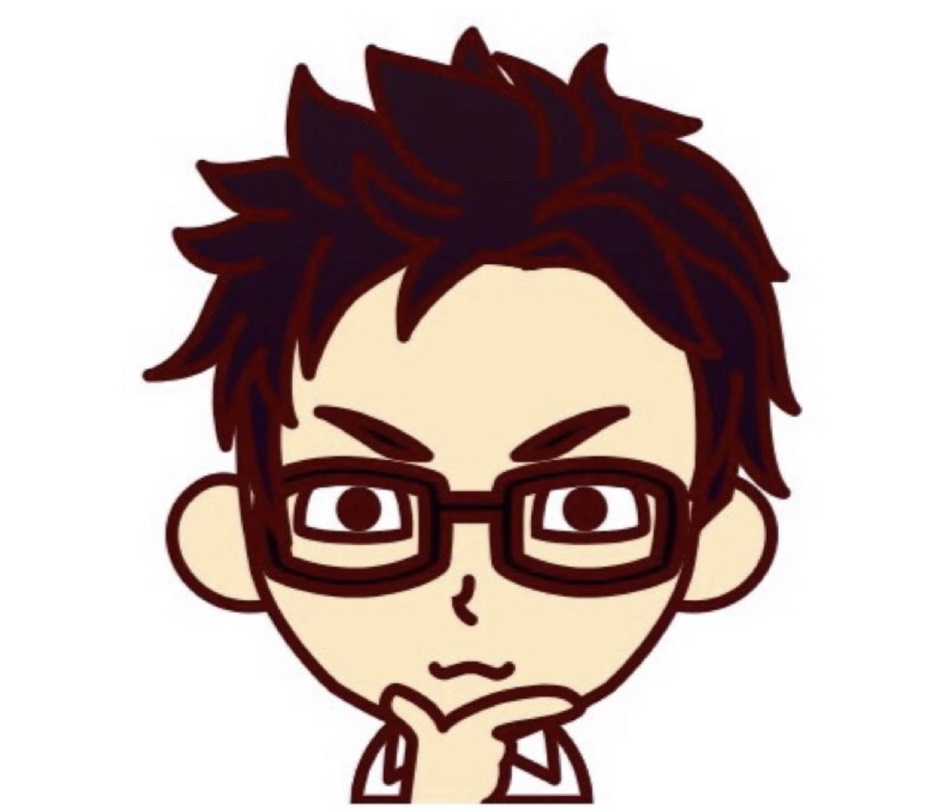